Evolution of synthetic rubber: bio-based raw materials and new types of rubber
Synthetic rubber is indispensable today, especially for car tires and technical rubber goods. Until now, the raw materials for its production have largely been obtained from fossil sources. Under the leadership of the Fraunhofer Institute for Applied Polymer Research IAP, four Fraunhofer Institutes are now developing alternative, bio-based raw material sources for synthetic rubber, which will enable completely new types of rubber for car tires. The three-year project is being funded by Fraunhofer with 3.25 million euros and starts in April 2024.
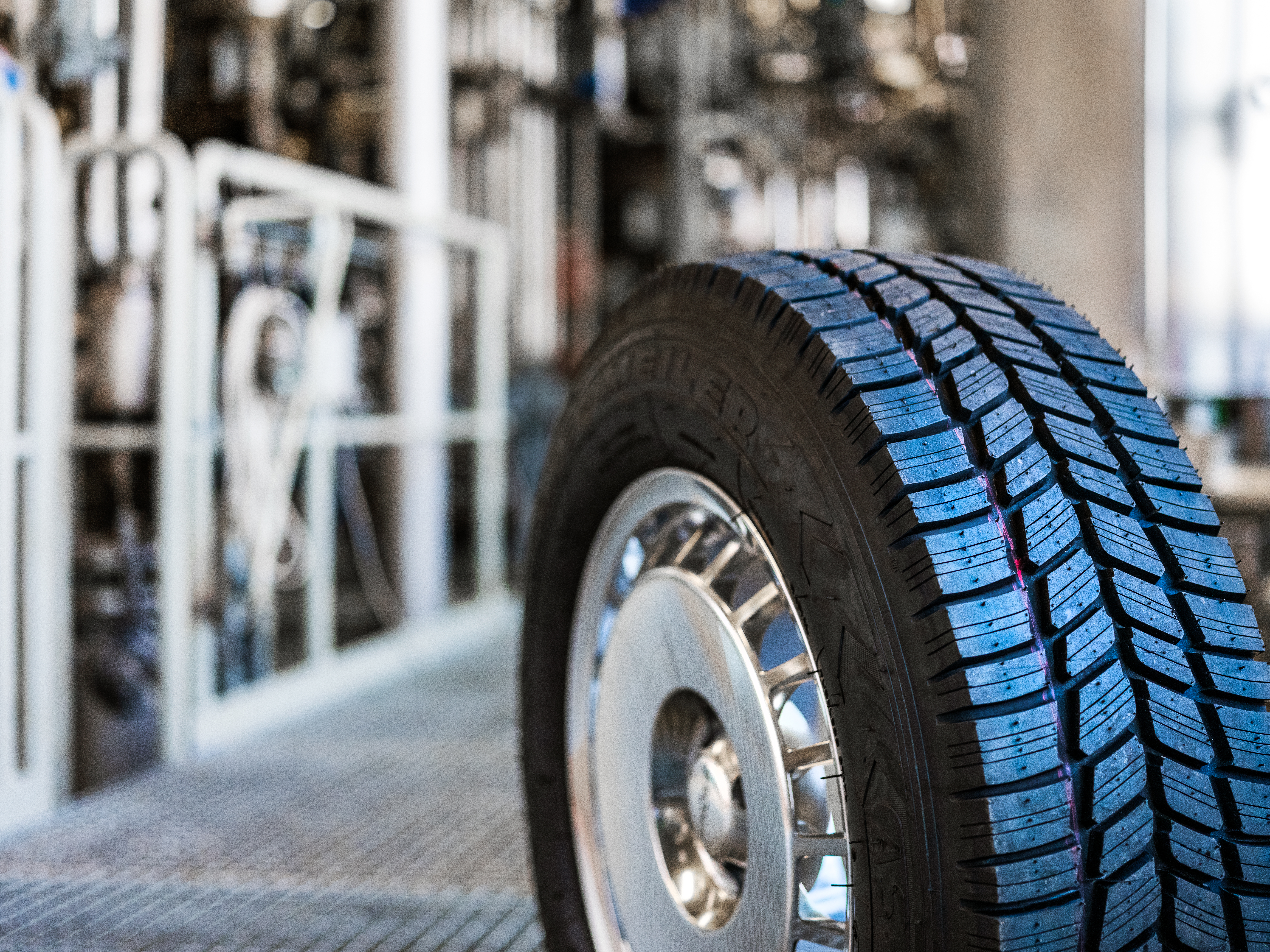
Almost 15 million tons of synthetic rubber are produced every year - and the trend is rising. At around 70 percent, car tires represent the main market for synthetic rubber. The required starting materials - the monomers butadiene, styrene and isoprene - are currently produced almost exclusively on the basis of crude oil. With the depletion of fossil resources and the urgent need to reduce CO2 emissions in the environment, there is an enormous need for sustainable alternatives for rubber producers worldwide. In addition, the aim of society to make mobility more sustainable is also placing new demands on car tires. These require advanced materials, design and production technologies.
Sustainable raw materials and innovative polymer structures
In order to meet these challenges, a team from four Fraunhofer Institutes is developing bio-based raw material sources for synthetic rubber as part of the project "Sustainable biomonomers for synthetic rubbers with application-related adjustable viscoelastic properties NaMoKau". The Fraunhofer Institutes for Applied Polymer Research IAP, for Microstructure of Materials and Systems IMWS, for Industrial Mathematics ITWM and for Environmental, Safety and Energy Technology UMSICHT are involved.
"In the project, we are producing the rubber monomers butadiene, isoprene and dimethylbutadiene from bio-based alcohols," explains Dr. Barbara Zeidler-Fandrich from Fraunhofer UMSICHT. "For this process to work, it is essential to use a catalyst that is as active and selective as possible. We are developing innovative materials based on clay minerals for this purpose."
"The production of sustainable dimethylbutadiene in particular is an outstanding feature of the project, as this monomer has not been available on a technical scale to date and is therefore not used in rubber production," adds NaMoKau project manager Dr. Ulrich Wendler, polymer expert at the Fraunhofer IAP. "We will make dimethylbutadiene accessible for rubber synthesis. Combined with the synthetic building blocks butadiene and isoprene, we will synthesize novel polymer structures with unique mechanical and thermal properties. This will create completely new types of bio-based rubber with material properties that were previously impossible to achieve and can be adjusted extremely systematically," says Wendler.
On the way to car tires with so far unprecedented properties
One of the major challenges in the development of car tires is to find an ideal balance between the three factors of rolling resistance, wet grip and abrasion. To improve these parameters, fillers, processing aids and other additives are added to the rubber. These have a significant influence on the tread of the car tire. "Our aim is to develop new compounds for car treads with so far unprecedented property profiles based on the rubber types that we will be researching in the project. This will open up new perspectives for the tire industry," explains Professor Mario Beiner from the Fraunhofer IMWS.
In order to achieve the market launch of the rubber as quickly as possible, the use of digital methods in material design is essential - for example to predict the properties of the complex rubber composites. "Using data-supported simulations, we make the most targeted suggestions possible for synthesis and material characterization tests. To this end, we are developing a software prototype for model-based prediction, uncertainty evaluation and test planning," says Professor Michael Bortz from Fraunhofer ITWM.
Ultimately, the developed materials will be used to create a fully testable tire demonstrator. "The entire value chain from the monomer to the polymer to the rubber compound used in the demonstrator will be accompanied by a life cycle assessment. This systematic analysis enables us to determine the ecological footprint in accordance with ISO and contribute to green chemistry," explains Dr. Markus Hiebel from Fraunhofer UMSICHT.
Evolution of synthetic rubber is progressing
With the NaMoKau project, the Fraunhofer researchers are consistently expanding their expertise in the field of synthetic rubber: "In an earlier cross-institute Fraunhofer project, we developed the biomimetic synthetic rubber BISYKA, which even exceeds the outstanding abrasion properties of natural rubber. The knowledge gained here in the field of synthesis and scale transfer is extremely helpful," explains Wendler. Thanks to the facilities at the Fraunhofer Pilot Plant Center for Polymer Synthesis and Processing PAZ, rubber production and compounding can be carried out on an industrial scale - an absolute plus point for industrial customers such as tire manufacturers, as well as producers of technical rubber goods or medical products.
"While we developed a synthetic rubber with as little abrasion as possible in the BISYKA project, we are addressing the ecological balance of synthetic rubber with NaMoKau. This is a meaningful and significant addition that fits perfectly with society's current efforts to reduce CO2 and microplastic emissions. In this way, we are continuing the development of sustainable synthetic rubber and driving its evolution forward," says Wendler.
Last modified: