3D printing of resins: fast curing with UV LED
A new 3D printing process, which should be clearly superior to the current processes in terms of print quality and speed as well as material homogeneity, is being developed in the research project "Belt deposited, double UV-cured materials for 3D engineering - overcoming the property limits of today's Rapid Manufacturing, BUERMa". Under the leadership of the Polymer Materials and Composites PYCO research division of the Fraunhofer Institute for Applied Polymer Research IAP, Freie Universität Berlin and Technische Hochschule Wildau are two Berlin-based companies working on the key technology of additive manufacturing (AM).
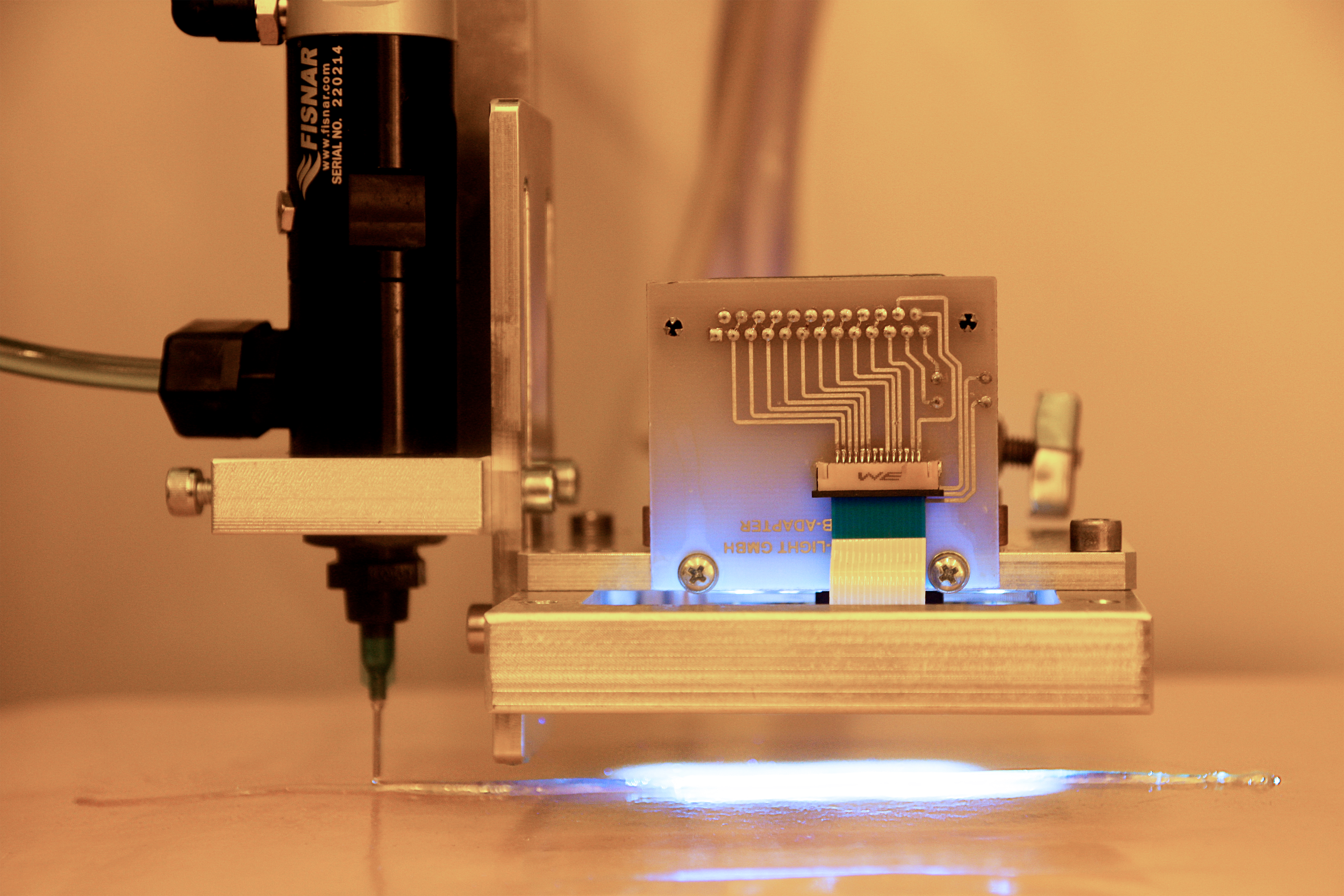
The research project aims to develop a novel 3D printing process that enables the simple, fast and efficient production of three-dimensional components using cost-effective UV-LED-curable reactive resins. This allows printing times to be significantly reduced compared to conventional additive manufacturing processes. In order to be able to manufacture highly resilient lightweight components, the use of reinforcing fibers, fillers, flame retardants and conductive additives will also be investigated. Additively manufactured components will thus be given improved properties and a wide variety of functionalities. The main focus is on the flexible and at the same time economical small series production of plastic components. The three-year project, which runs until December 2021, is funded by the Federal Ministry of Education and Research as part of the 2020 - Partnership for Innovation programme within the Advanced UV for Life consortium (FKZ 03ZZ0145A). The kick-off event took place on 13 September 2019.
What are the advantages of the BUERMa process?
The BUERMa process has clear advantages over established additive manufacturing processes such as Fused Deposition Modeling (FDM), which is often used. The FDM process currently uses thermoplastics, i.e. plastics that have to be heated to allow them to be deformed and cooled down again after the component has been manufactured. These materials have unavoidable disadvantages: For example, the warp effect, which causes the component to warp uncontrollably during cooling. In addition, FDM components usually have a much lower resistance to external environmental influences. In the BUERMa project, on the other hand, synthetic resins are used. They cure by UV irradiation to form a polymer network known as duromers. Once cured, they can hardly be deformed as a result of heating. They therefore have significantly higher heat resistance, which means that components can be manufactured in more detail. The BUERMa process also has clear advantages over other radiation-based 3D printing processes, such as stereolithography (SLA): fewer process steps, lower machine costs, less post-processing of printed products and much more cost-effective polymer materials.
"With the new process, we want to overcome the disadvantages of thermoplastic materials, which are strongly represented on the market. With duromers, for example, a higher production speed is expected, since the printed components are cured directly as they leave the printing nozzle by means of UV LEDs. Furthermore, the process is expected to be more cost-effective than the established processes and to have far higher component precision," explains Professor Christian Dreyer, Deputy Head of the Polymer Materials and Composite PYCO research division at the Fraunhofer IAP, who is leading the project. "In addition, it is our goal to make the process fit for industrial series production beyond rapid prototyping," says Dreyer.
How are resins printed?
In the BUERMa process, a viscous reactive resin is mixed with a photoinitiator, introduced into a metering unit and pressed through a nozzle with a diameter of 0.1 to 0.6 millimeters. The material is then deposited in pre-programmed tracks and directly irradiated with UV LEDs. This process ensures that the resins cross-link with the aid of the photoinitiator and form an extremely stable polymer network - they cure immediately in a controlled manner. The layers are then built up in layers, as in the FDM process, for example.
"Crosslinking is an extremely fast process. The resin cures quasi at the moment the UV light penetrates. This means that the printed component can only warp slightly and can be printed even faster," says Dreyer. He has already demonstrated in preliminary studies that this principle works in principle. In the project, the research team not only wants to develop a robust printer system for industrial applications, but also specially adapted resin formulations for various technical applications. Investigations are also planned to determine optimal process windows and parameters. Important factors influencing quality are the printing and conveying speed, the dosing method, the viscosity of the resin, the UV intensity and the irradiation method. Within the scope of the project, a compact print head equipped with UV LEDs will be designed and developed.
Who is involved in the development?
Simulations of the printing process and UV irradiation as well as preliminary tests on 3D printers in the laboratory will be carried out at TH Wildau. The resins are printed on an FDM printer from Karl Rabofsky GmbH / PYOT Labs GmbH, which is further developed for the special requirements. The dispenser technology of the print head, with which the viscous resin is to be dosed, is being developed in the PYCO research division of the Fraunhofer IAP. The optimal process parameters are also determined here. The properties of the printed materials and the handling of the newly developed 3D printing systems will then be investigated at Bernhardt Kunststoffverarbeitungs-GmbH in Berlin and at TH Wildau and optimized together with the project partners. Here, the components produced with the new process are to be compared with conventionally manufactured components, possible barriers for a rapid introduction of the process into practice are to be identified and overcome by suitable modification of the process.
Last modified: