K 2019
Bio-based carbon fibers –
high-performance and sustainability for light-weight applications
Carbon fibers are made from fibrous polymer precursors. Petroleum-based polyacrylonitrile (PAN) is the precursor used for 95 percent of the carbon fibers on the world market. Precursors made from renewable raw materials are currently being developed at the Fraunhofer Institute for Applied Polymer Research IAP in Potsdam. A new oven, which generates temperatures of up to 2900 °C, now makes it possible to produce bio-based carbon fibers whose properties partially achieve those of conventional PAN-based carbon fibers. The Fraunhofer IAP will be presenting various innovative precursor materials at the K Trade Fair in Düsseldorf from October 16 to 23, 2019. Visit the Fraunhofer IAP at K 2019: Hall 7, Stand SC01
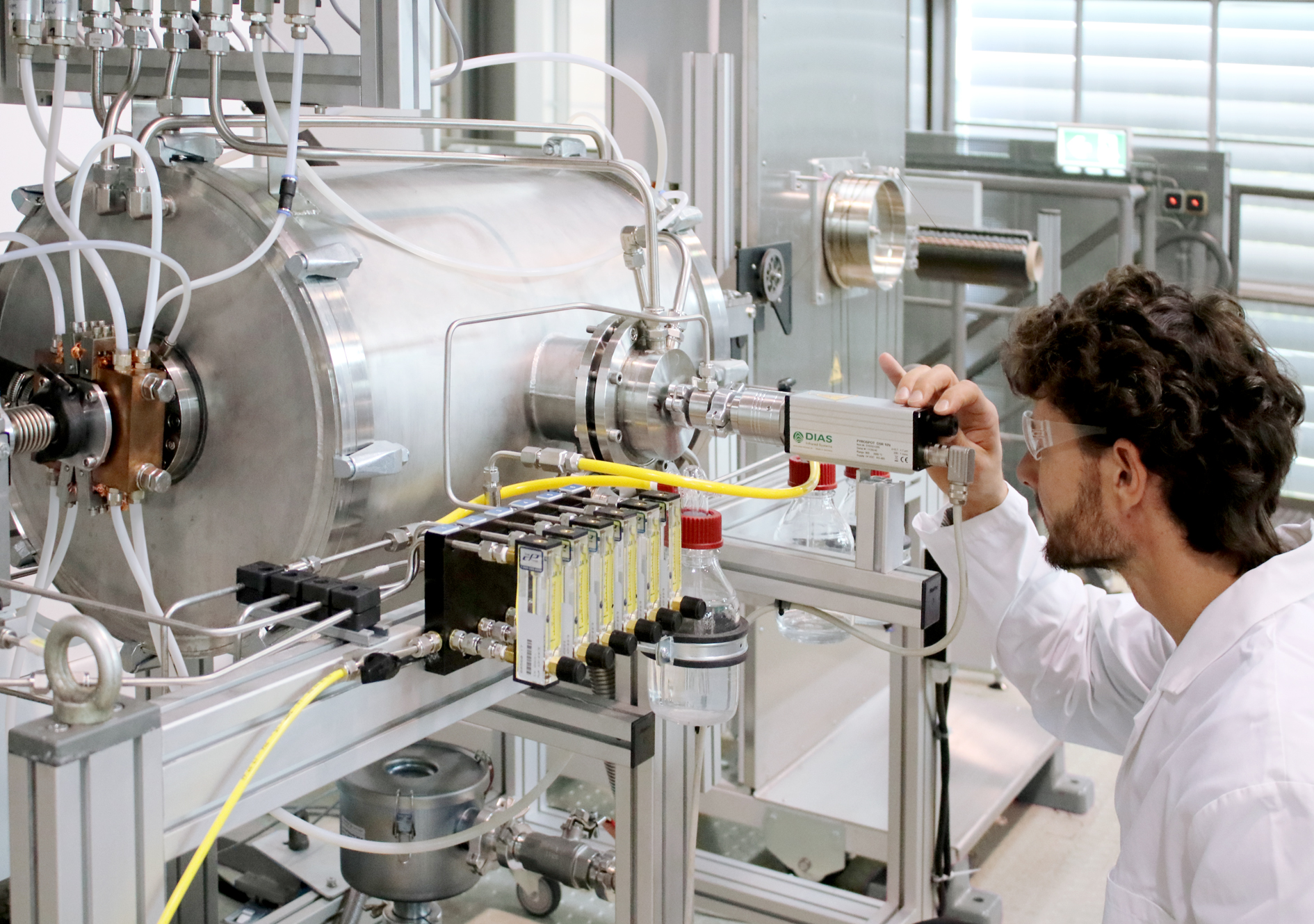
Carbon fibers represent the strongest and stiffest material that can currently be produced in industrial-scale plants. These properties and their low weight make them indispensable today, especially as a reinforcement for plastics in lightweight construction applications. They are excellent for components that undergo high levels of stress in, for example, airplanes, cars, sporting equipment and wind turbines. In the future, the size of wind turbines will increase in order to meet the demand for alternative energies. In the area of alternative mobility, carbon fibers will be used as a lightweight reinforcement material in the hydrogen tanks of cars, for example. Another important field of application for carbon fibers is the construction industry. So-called carbon concrete is lighter than conventional reinforced concrete and does not corrode. Today it is already being used to build and sustainably renovate crumbling bridges.
In terms of global environmental aspects, the demand for bio-based and sustainable high-performance materials is steadily growing in the field of lightweight construction, also in support of future green technologies. However, high-performance carbon fibers made from renewable raw materials are almost completely absent from the market.
Bio-based carbon fibers – what challenges do they face?
Achieving a carbon fiber which almost exclusively consists of carbon, a loop way over a malleable precursor has to path since pure carbon is neither soluble nor meltable. Therefore, it cannot be converted directly into fiberous form. "The production of carbon fibers from precursors based on renewable raw materials like cellulose, lignin or hemicellulose is possible in principle, but common pyrolysis temperatures of up to 1600 °C limit mechanical properties such as stiffness and strength. These bio-based carbon fibers do not represent a serious alternative to their petroleum-based counterparts in high-performance applications," explains Dr. Jens Erdmann, a fiber expert at the Fraunhofer IAP.
In order to produce bio-based carbon fibers for high performance applications, some hurdles need to be overcome: 1. Poor material yield. Depending on the bio-based raw material, only about 10 to 30 weight percent of the precursor currently turns to carbon fiber. The waste products are lost as a gaseous fraction when the precursor is thermally converted to carbon fiber. 2. The low ratio of ordered carbon structures in the carbon fiber. 3. The low alignment of the ordered carbon structures along the fiber axis. This is the crucial determinant of the fibers’ properties. "At the Fraunhofer IAP, we are addressing all three hurdles and finding practical and cost-effective solutions in cooperation with partners from industry," says Erdmann.
Properties improve after undergoing a few seconds of extreme temperatures
“The greatest challenge, however, is to considerably boost the bio-based carbon fibers’ mechanical properties, in particular their strength and stiffness,“ says Erdmann. “To do this, we had a special ultra high temperature oven built in which the bio-based carbon fibers are post-treated for a few seconds at temperatures of between 2700 and 2900 °C. In this temperature range, the carbon structures in the fiber are stretched so that they align along the fiber axis. This makes the fibers much stronger and stiffer and produces mechanical properties on par with those of petroleum-based carbon fibers. This enables us to produce so-called high modulus fibers“, says Erdmann.
The principle behind the ultra high temperature oven is similar to that of an incandescent light bulb in which electrical current is conducted through a filigree carbon filament until it becomes so hot that it glows. The oven is much larger than an incandescent light bulb and instead of the carbon filament, it has a solid graphite tube that serves as a heating element. Depending on the desired temperature, a current of up to 1500 amperes is passed through it until it glows. The carbon fiber is transported through the tube and stretched in a precise way. One vital element is the inert gas atmosphere that protects both the oven and the fiber from thermo-oxidative decomposition.
Research for industrial clients
The new oven provides the Fraunhofer IAP, and thus also its cooperation partners, with many new opportunities for developing stable, lightweight materials. Its current research – the production of fibers from solutions and melts, the modification of biopolymers, polymer synthesis, thermal conversion and analysis as well as material and structure characterization - are optimally supplemented by the production and development of high-performance carbon fibers.
“Past experience has shown that companies requiring research and development services in the field of ultra high temperature fiber treatment have struggled to find a partner with an ultra high temperature oven. The Fraunhofer IAP can now offer this. The oven is well-suited for the testing of many different parameters in a short time using little amounts of fiber material,” Jens Erdmann is happy to report.
Last modified: