Microencapsulated additives: novel filaments for 3D printing
3D printing is becoming increasingly important in the manufacture of prototypes and the production of final components. Additives such as colorants and fragrances, fillers and lubricants or biocides give the printed plastic objects individual functional properties. Incorporating these additives into the plastic is often not easy, as many additives are not suitable for the filament-based 3D printing process. The SKZ and the Fraunhofer Institute for Applied Polymer Research IAP are therefore using microencapsulation to make a wide range of additives available for 3D printing filaments.
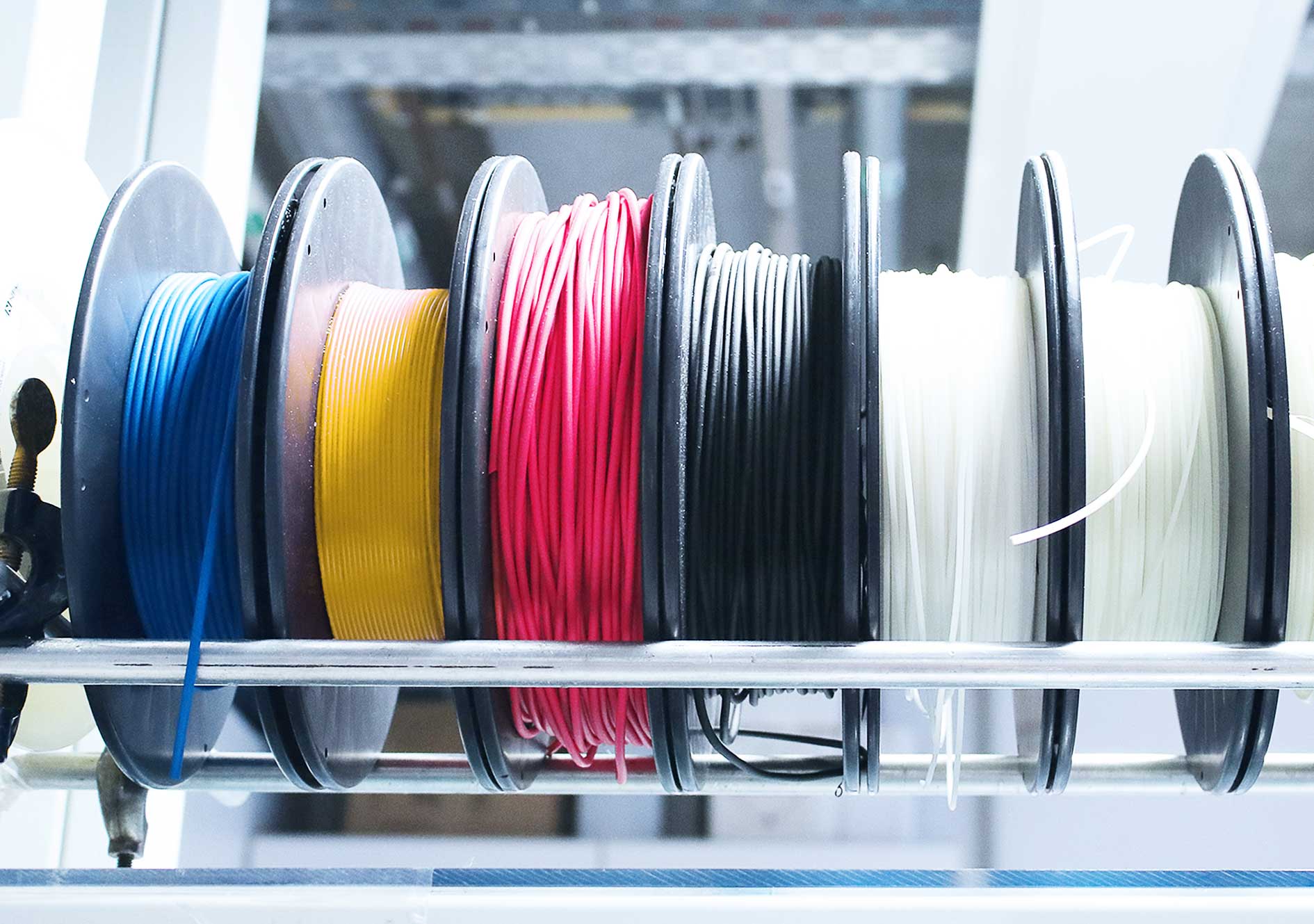
SKZ and Fraunhofer IAP with joint project
Additive manufacturing or 3D printing is now standard in industrial product development. Wherever individualized components in small quantities and complex or intricate geometries are required, it is increasingly unfolding its potential. In addition to the right manufacturing and production method, customized materials are a decisive factor for successful use. However, the choice of materials for filament-based 3D printing is still limited. The SKZ Plastics Center and the Fraunhofer IAP have therefore set themselves the goal of significantly expanding the range of filament materials by adding additives in order to further exploit the technological and economic potential of this technology. "The highlight is that we will also incorporate microencapsulated additives such as lubricants into filaments. This gives the printed component a new function: it can lubricate itself," explains Dr. Alexandra Latnikova, a specialist in microencapsulation at the Fraunhofer IAP. "However, not just any additive is suitable for this, as filament-based 3D printing techniques have their limits," says Latnikova.
Challenge: Material development for filament-based 3D printing
In filament-based 3D printing - known as fused layer modeling (FLM) or fused filament fabrication (FFF) for short - a strand of plastic, the filament, is melted in a hotend, pressed through a nozzle and deposited in thin layers on a build platform. The filament is made of plastic, which softens when heated and can only pass through the nozzle in this state. "This is precisely where the challenge lies, because if additives have been incorporated into the filament, there are particles in it that can clump together and lead to blockages in the nozzle. The nozzle is therefore the limiting factor. In our extensive investigations, we will determine with which additives 3D printing is possible," explains Latnikova.
Screening of additives: from solid to liquid
As a first step, the research team is systematically testing which commercial and self-developed polymer additives are fundamentally suitable for the production of filaments and the printing process. "We investigate characteristics such as particle size, surface properties, thermal stability and filling level and test the limits of the possibilities. In the second step, we use our specially developed microcapsules," explains Patrick Limbach, material developer at the SKZ. The Fraunhofer IAP contributes its extensive know-how to microencapsulation. This technology also makes it possible to produce more complex additives. To do this, the scientists encase functional additives in a thin polymer wall. In this way, liquids such as lubricants, fragrances and colorants or even biocides can be incorporated into plastics. The size, thermal stability and surface properties of these particles are tailor-made. "We give the materials many smart functions. For example, microencapsulated dyes can indicate defects in printed components, as color leaks out when the capsules in the material are damaged. In a previous project, we have already successfully demonstrated that microencapsulated lubricants give injection molded components self-lubricating properties. This can reduce material wear, which is normally caused by friction on components, by up to 85 percent. We are now transferring these results to 3D printing," says Limbach.
Strengthening the innovative power of German SMEs: companies welcome
With this research, the project network aims to strengthen the innovative power of German SMEs in the field of material development for additive manufacturing. "Our aim is to increase customer acceptance of 3D printing processes and market diversification with a wide range of highly functional filament materials. For small and medium-sized companies, these application-specific specialty materials should make it easier to get started with additive manufacturing. We invite interested companies to join our project committee, contribute suggestions and ideas and participate in the results," explain Latnikova and Limbach. The project is primarily aimed at companies that are part of the production chain for filament-based 3D printing, i.e. microcapsulators, manufacturers and distributors of plastic additives, compounders, manufacturers of plant systems and service providers in the field of filament-based 3D printing.
About the project:
The two-year research project, which started in June 2021 with the funding code 21817 BG, is funded by the Federal Ministry for Economic Affairs and Energy (BMWi) via the SKZ e. V. funding association and the German Federation of Industrial Research Associations (AiF) as part of the program for the promotion of joint industrial research (IGF) on the basis of a resolution of the German Bundestag.
Last modified: