Solar modules embedded in glass
Organic solar modules have advantages over silicon solar cells. However, one critical problem is their shorter operating life. Researchers are working on a promising solution: they are using flexible glass as a carrier substrate that better protects the components.
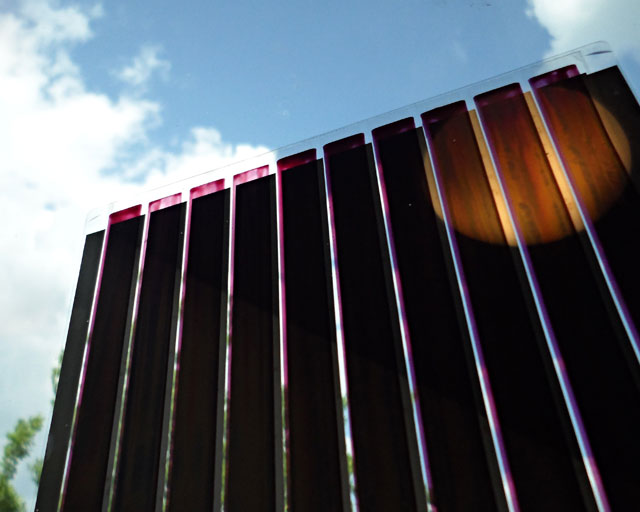
This approach is already being employed in electronic devices to some extent today: organic photovoltaics (OPVs) are embedded in film. These OPVs are a promising alternative to silicon-based solar cells. The materials can also be processed at atmospheric pressure. However, the main advantage is the modules can be manufactured using printing technology – this is faster and more efficient that the involved processes necessary for fabrication of inorganic components. A flexible type of substrate material is necessary for fabrication that uses a printing process. Polymer films that have certain serious disadvantages have been employed up to now. The films are somewhat permeable to humidity and oxygen. Both of these attack the sensitive solar modules and significantly reduce their operating life. Up to now, substrates with barrier layers have protected the OPV modules, depending on the application. For higher processing temperatures and longer operating life, different carrier substrates must be used.
Fracture-resistant and extremely strong
Researchers of the Fraunhofer Institute for Applied Polymer Research IAP in Potsdam, Germany, are working with a new carrier material at present. They are embedding the solar modules in a thin layer of glass. “Glass is not only the ideal encapsulating material, it also tolerates process temperatures of up to 400 degrees,” explains Danny Krautz, project manager in the Functional Materials and Components research section at IAP. A specialized glass from Corning Inc. is being employed in the research work. Thanks to its special physical properties, layers can be made that are only 100 micrometers thick. That corresponds roughly to the thickness of a sheet of paper and has nothing to do with the type used to make drinking glasses. The special glass is not only fracture-resistant and extremely strong, it is so flexible that it can be gently bowed even in its solid form. The researchers in Potsdam in cooperation with their partner Corning have already created the first working OPVs with this material by processing stacks sheet-by-sheet.
Production on rolls
The goal is to fabricate these modules in rolls as well. The carrier substrate will be wound on a roll in this case, similar to how newspapers are printed. An empty roll is positioned opposite it. The photoactive layers and electrodes are printed in several steps between the two rolls. Large surfaces can be manufactured effectively in series using this fabrication technology. The team from IAP has already begun a first test of how the flexible glass could be processed in this way. “We were immediately successful on our first run in producing homogenous layers on smaller substrate dimensions,” according to the scientist. The technology needs to be modified at many points for the process to meet the demands of industrial applications – and the Potsdam team is already working on these. Long-lived, robust, high-performance OPVs can be fabricated with this technology for use in a wide range of applications – from tiny solar cells in mobile phones to large-scale photovoltaic modules.
Last modified: