Bioplastics in everyday education – new types of PLA are now market fit
Soon pupils will not only learn about bioplastics in chemistry class, they will be able to grasp them with their hands. In the future, the building blocks in the molecule construction kit produced by Cornelsen Experimenta GmbH will be made of bioplastics. The Fraunhofer Institute for Applied Polymer Research IAP in Potsdam-Golm is assisting in the development of these materials. Along with three other companies from the plastics sector in Brandenburg and Berlin - Uhde Inventa-Fischer GmbH in Berlin, Linotech GmbH in Guben and Hesco Kunststoffverarbeitung GmbH in Luckenwalde – the institute is developing and making ready for the market new types of the bioplastic called polylactic acid (PLA).
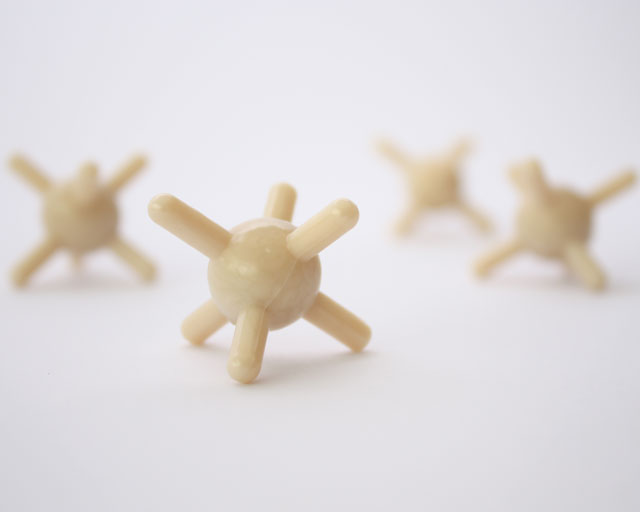
Polylactic acid is a bioplastic that is already being used in everyday products such as children’s toys. However several of the properties of commercial PLA - such as dimensional stability under heat - still have room for improvement. The material changes form at temperatures as low as 60 °C. Conventional PLA is not suitable, for instance, for ball point pens that have been left in cars in the summer, or children’s toys that should be cleaned in the dishwasher. 96% to 98% of it is made up of lactic acid units that rotate clockwise, like those found in yogurt. The remaining lactic acid units rotate counterclockwise and are randomly distributed throughout the chain. This structure is responsible for its light deformability, even at relatively low temperatures.
In order to rectify this problem, the Fraunhofer IAP and Uhde Inventa-Fischer GmbH have developed two new types of PLA as part of a project funded by the EU and the Ministry for Economics and European Affairs of the State of Brandenburg. "We have linked together lactic acid units in a new way," explains Dr. Antje Lieske, a polymer researcher at the Fraunhofer IAP. "This has resulted in two new types of PLA. Type 1 is called c-PLA. It is made entirely of clockwise rotating lactic acid units which are arranged like beads on a string. The second type is called sb-PLA. It is made up of two kinds of strings of beads that consist of either 100 beads of clockwise rotating or 100 beads of counterclockwise rotating lactic acid units. The two strings are always alternately linked to one another," says Lieske. c-PLA is synthesized at the demonstration pilot plant at Uhde Inventa-Fischer in Guben, which can produce up to 500 tons of PLA annually. The Fraunhofer IAP uses a miniplant to synthesize sb-PLA. It is not designed to produce large quantities, however it can be very flexibly adapted to the process.
In a second step, Linotech GmbH adds special additives to the two new types of PLA to make them impact resistant. "This step is very important so that the PLA product is able to withstand high mechanical stress. One thing we develop is compounds for toys made from renewable raw materials. It’s easy to imagine how important impact resistant materials are in this context," explains Linotech’s CEO Cord Grashorn.
In the final step, Hesco Kunststoffverarbeitung GmbH produces and tests - with success - the test object: a sulfur atom made from a molecule construction kit consisting of both PLA types. c- and sb-PLA that have been modified for impact resistance are dimensionally stable at temperatures of 75 °C and 90 °C respectively. They also crystallize faster than conventional PLA. Moreover, sb PLA can be processed almost as well as the petroleum-based plastic acrylonitrile butadiene styrene (in short ABS) which is currently in use.
Hesco CEO Birgitt Reiche remarks, "The investigated sb-PLA fulfills the requirements of this goal superbly. Naturally the price of biobased products used on an industrial scale is a very decisive factor." In order for a new type of PLA to be competitive on the market, the injection molding process has to be made considerably more cost-effective. Furthermore, the Fraunhofer IAP is currently working on drastically simplifying the process for manufacturing sb-PLA.
Last modified: