Interview
Recycling of synthetic polymers
Recycling is essential to achieve a circular economy for plastics. Up to now, mechanical methods have mainly been used to process waste plastics into recycling granulate, so-called recyclate, which can be reused as a raw material for new products. Scientists at Fraunhofer IAP are also developing approaches to recover the chemical building blocks of plastic products. Monomers constitute the focus of our attention. These can be used to produce new, high-quality polymers. Their repeated use reduces our dependency on fossil raw materials. Dr.-Ing. Marcus Vater explains current developments and fields of action at the institute.
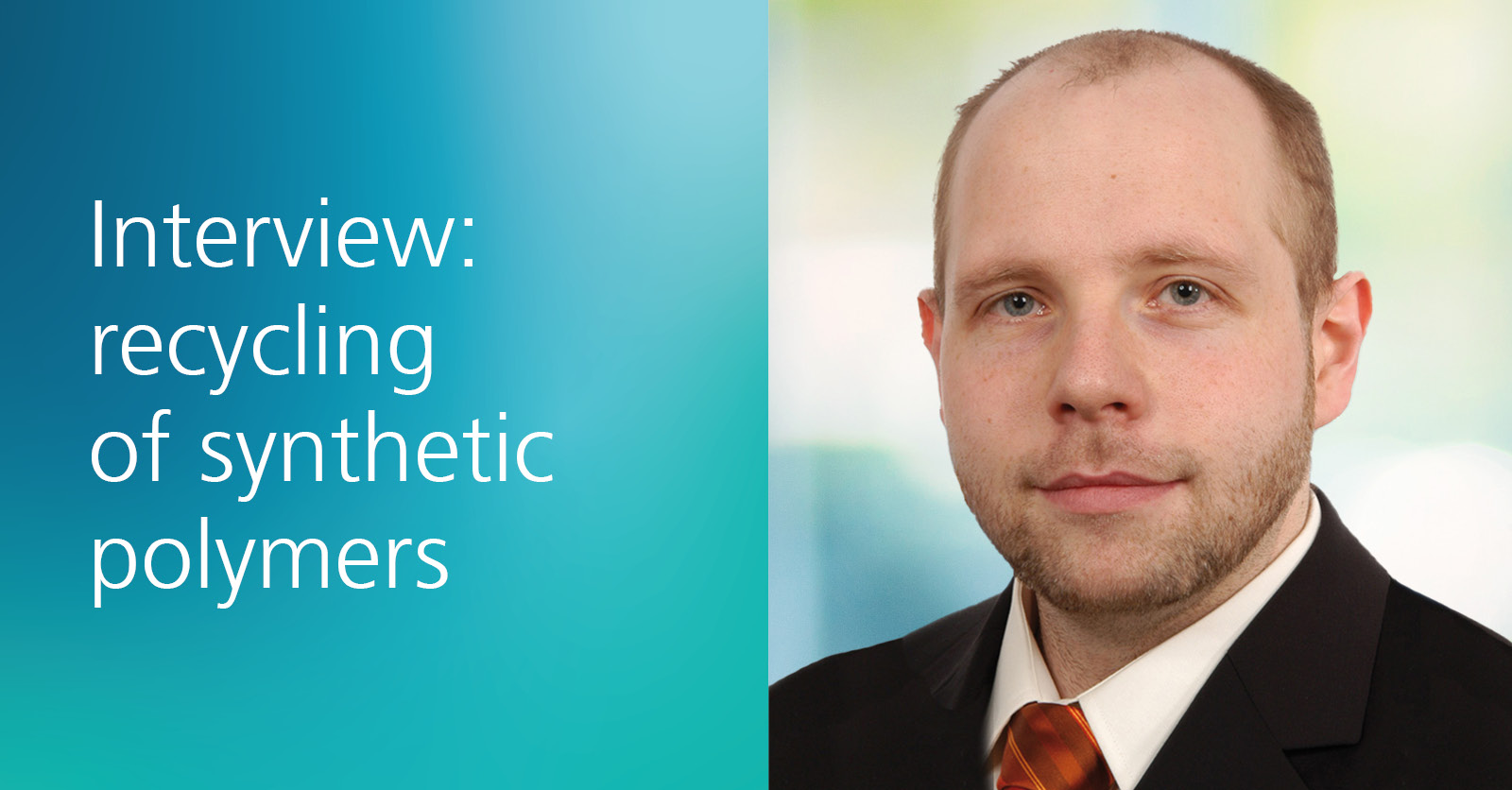
A 50 percent recycling quota for packaging and a 25 percent recycled content in bottles by 2025 – these are the requirements of the European Union’s Circular Economy Package and Germany’s Packaging Act. This means that industry needs to take quick action and improve recycling concepts. How is Fraunhofer IAP supporting its customers in achieving these goals?
Marcus Vater: We collaborate with partners from industry on recycling projects for plastics based on polyamide and polyester, for example. One project that has occupied us for several years is the validation of recycled monomers, for example for polyethylene terephthalate, or PET for short. PET is a polyester-based material used to make bottles, fibers and films. We are the port of call for industrial customers who are developing recycling processes and recovering the monomer terephthalic acid contained in PET. We also cater to manufacturers of PET who are offered the monomer on the recycling market. We use the recovered terephthalic acid to produce polymers in various quantities. Small quantities starting at 25 grams can be used to test suitability. Quantities up to six kilograms are used to characterize mechanical properties and colors. We also synthesize research samples of up to 1,000 kilograms. Our customers test whether the PET can be reprocessed with the recycled monomers into a suitable bottle or fiber. We are currently developing our own recycling process for another polyester, polybutylene succinate, which goes by the abbreviation PBS.
“Chemical recycling is a growing field of research and development. One of the major challenges is to recover monomers that have a high degree of purity.”
What obstacles need to be overcome in the development of chemical recycling processes?
Chemical recycling is a growing field of research and development. One of the major challenges is to recover monomers that have a high degree of purity. This is imperative if new, high-quality polymers are to be produced from them. Removing ink residues, stabilizers and detergents, for example, is part of the recycling process. This requires the development of new purification processes. Our many years of experience in the synthesis and process development of polymers forms the foundation for this. Our goal is to design a monomer cycle with as little loss of mass and quality as possible.
Industries such as the automotive and aviation industries are also looking for recycling solutions. Which activities does Fraunhofer IAP pursue in this regard? What services do you offer?
We work closely with industry in the field of thermosets and thermoplastics. For example, we provide the expertise for those who are interested in knowing the exact properties of their recyclate and which applications it can be used for. We specialize in the evaluation of plastic materials. When it comes to recycling a component made of a composite material – for example the rotor blades of a wind turbine – we are able to chemically recycle the plastic matrix and retain the fibers so that this high-quality material can be reused.
You are greatly committed to further developing the recycling competencies of Fraunhofer IAP. What is your personal vision of the plastic cycle in 2050?
In 2050, the plastic cycle will be close looped. Unavoidable losses will no longer be a problem, as plastics will be fully biodegradable and losses will be compensated for by renewable resources. Once we have achieved this vision in 2050, I can look forward to retiring with a smile.
Last modified: