Kleidung aus Baumwolle effizient recyceln
Neues T-Shirt aus alter Jeans
Kleidung aus Baumwolle zu recyceln war bislang technisch nicht möglich. Einem Forscherteam des Fraunhofer-Instituts für Angewandte Polymerforschung IAP ist es jetzt erstmals gemeinsam mit einem schwedischen Unternehmen gelungen, aus recycelter Baumwolle ein Viskose-Filamentgarn herzustellen. Die Textilfaser eignet sich sogar für die Fertigung in Großserie.
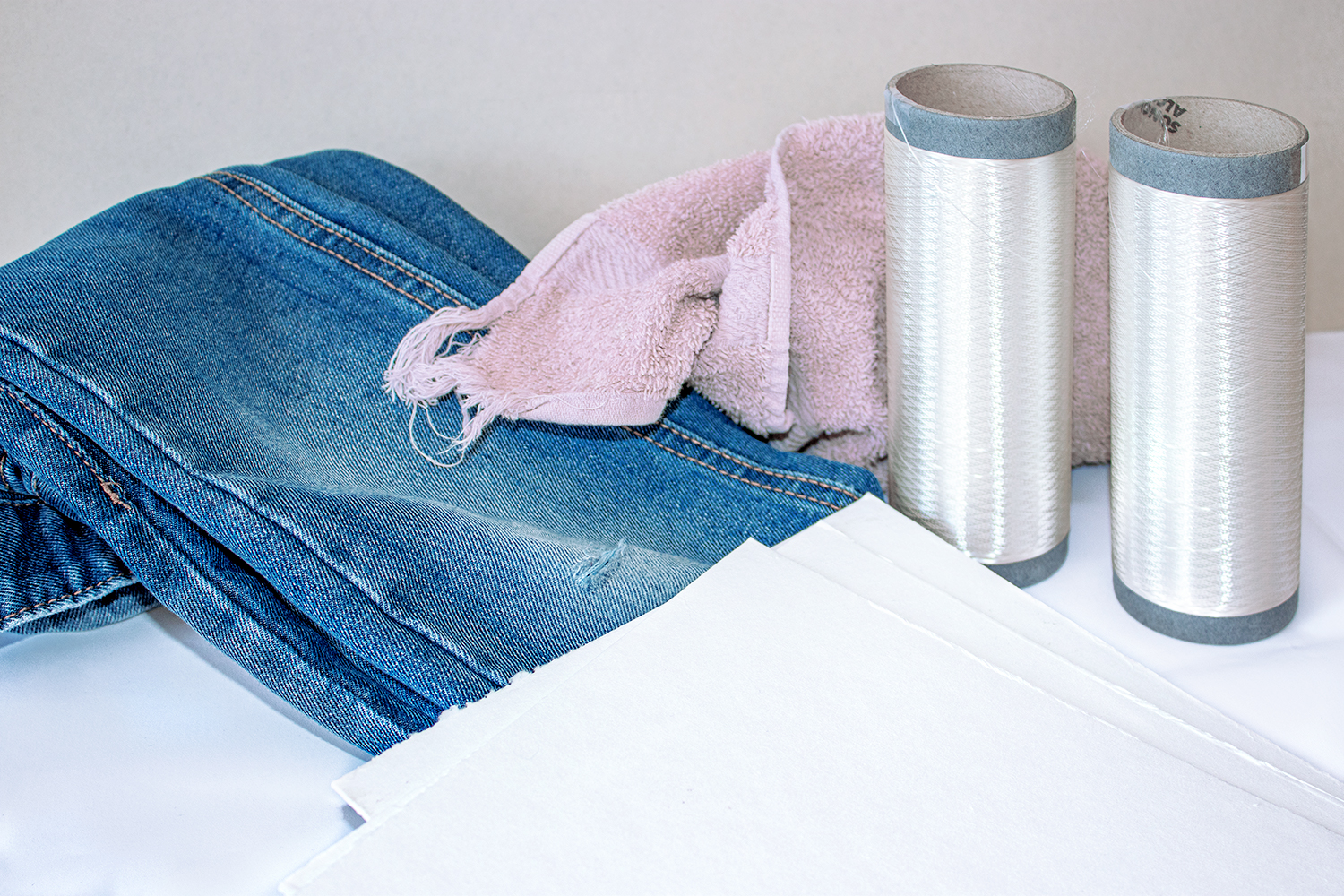
Nicht wenige Kleiderschränke quellen über. Dabei werden viele Hosen, Röcke und Oberteile kaum oder gar nicht getragen, so das Ergebnis einer Umfrage von Greenpeace zum Kaufverhalten der Bürger. Selbst nicht beschädigte Kleidung wird aussortiert und landet in der Mülltonne oder Altkleidersammlung. Umweltfreundlich ist das nicht – Unmengen an Ressourcen, Chemikalien und Wasser fallen für die Herstellung von Kleidung an. Zwar werden Altkleider hierzulande wiederverwertet – zu minderwertigen Produkten wie Reinigungstüchern, aber nicht zu neuen Kleidungsstücken. Der Grund: Hosen, Hemden und Co. sind selten sortenrein, sondern bestehen aus Mischgewebe. Die miteinander verwobenen Fasern zu trennen, ist bislang nicht möglich gewesen. »Textilien bestehen selten aus reiner Baumwolle. Eine Jeans etwa enthält immer einen Anteil an Chemiefasern wie Polyester oder Elasthan«, sagt André Lehmann, Wissenschaftler am Fraunhofer IAP in Potsdam. Im Auftrag des schwedischen Unternehmens re:newcell ist es dem Chemiker und seinem Team nun gelungen, Zellstoff aus recycelter Baumwolle zu Viskosefasern aus reiner Cellulose weiterzuverarbeiten.
Neues Viskose-Filamentgarn so gut wie holzbasierte Cellulosefasern
Üblicherweise wird Zellstoff von der Textilindustrie als Ausgangsmaterial verwendet, um daraus künstliche Celluloseregeneratfasern wie Viskose, Modal oder Lyocell herzustellen. Da der Zellstoff nicht schmelzbar ist, muss dieser zu einer Spinnlösung aufgelöst und zu cellulosischen Spinnfasern umgeformt werden. Der Zellstoff wird in der Regel aus Holz gewonnen. »Wir haben von re:newcell jedoch Zellstoffplatten aus recycelter Baumwolle erhalten und sollten prüfen, ob sie sich zu Viskosefasern weiterverarbeiten lassen. Durch Einstellen der richtigen Parameter im Lösungs- als auch Spinnprozess, wie effektive Filtrationsstufen, konnten wir die im Zellstoff enthaltenen Fremdfasern herauslösen«, so der Forscher. Das Ergebnis: Ein Filamentgarn, also eine mehrere Kilometer lange Endlosfaser, die zu 100 Prozent aus Cellulose besteht und qualitativ vergleichbar ist mit holzbasierten Celluloseregeneratfasern. Aus dem Baumwoll-Zellstoff konnten im Spinnverfahren neue Fasern hergestellt werden, die sich für die Massenfertigung im industriell etablierten Viskoseprozess eignen. »Wir konnten den hohen Anspruch von re:newcell an die Reinheit der neuen Faser erfüllen«, sagt Lehmann, der das ent-standene Filamentgarn als baumwollbasierte cellulosische Regeneratfaser bezeichnet. Im Vergleich mit marktüblichen Viskosefasern konnte diese überzeugen und wies dieselben Eigenschaften auf.
Das war keine leichte Aufgabe, denn das Viskoseverfahren ist komplex: Zunächst muss der Zellstoff mit Lauge aktiviert und anschließend chemisch derivatisiert werden. Auf diese Weise erhält man eine hochreine alkalische Viskose-Lösung, die mittels Spinndüsen, die mehrere tausend Spinnlöcher mit Durchmessern von 55 μm aufweisen, in ein saures Spinnbad ausgesponnen wird. Aus den jeweils zu tausenden sich bildenden Flüssigkeitsfädchen der polymeren Lösung regeneriert sich die derivatiserte Cellulose und fällt kontinuierlich in Fadenform im Spinnbad aus. Im weiteren laufenden Prozess wird die chemische Derivatisierung beständig rückgängig gemacht und der Faden weitergewaschen, bevor man ihn getrocknet aufspult. Er besteht dann aus reiner Cellulose. Damit ist er umweltfreundlich, denn Cellulose verrottet und trägt nicht zu den Bergen an Mikroplastik bei, die die Weltmeere verschmutzen. Ein großer Vorteil gegenüber erdöl-basierten Polyesterfasern, die noch mit einem Anteil von rund 60 Prozent auf dem Weltmarkt dominieren.
Mehr Nachhaltigkeit in der Mode
»In der Regel wird Baumwoll-Kleidung verbrannt oder sie landet auf der Deponie. Künftig kann sie mehrfach wiederverwertet werden und so zu mehr Nachhaltigkeit in der Mode beitragen«, sagt Lehmann. Darüber hinaus ist es so möglich, die Rohstoffbasis für die Zellstoffgewinnung der Textilindustrie zu erweitern. »Bisher ist die holzbasierte Cellulose der Ausgangsstoff für Viskosefasern. Durch das Optimieren der Trenn-prozesse und die Intensivierung der Filtration der Fremdfasern im Spinnverfahren können wir langfristig die rezyklisierte Naturfaser-Baumwolle als alternative Zellstoffquelle und ernst zu nehmende Rohstoffbasis etablieren.«
Letzte Änderung: